Bimetal Band Saw Blade
Are you seeking unmatched quality in bi-metal bandsaw blades? With YISHANHN, experience the confidence that comes from reliable performance, fast delivery, and exceptional value. Our commitment to tailored solutions ensures your unique needs are met with blades engineered for optimal cutting performance and extended durability. Trust YISHAN to supply superior bandsaw blades that drive the success of your business.
Your Trusted Supplier of Bimetal Band Saw Blade
Welcome to YISHANHN, your source for advanced bi-metal bandsaw blades known for durability and precise cutting performance. Our blades are designed to maximize efficiency and minimize downtime, making them ideal for distributors and agents serving demanding industries.
Choose from a wide range of blade types, including widths, tooth, and materials, all crafted to suit your customers’ unique cutting needs. Whether you’re supplying blades for metalworking, woodworking, or construction, our products deliver reliable, efficient results that keep operations running smoothly.
Trust YISHANHN for top-quality bandsaw blades that enhance performance across industries. Partner with us to deliver consistent, long-lasting solutions that drive your success in the market.
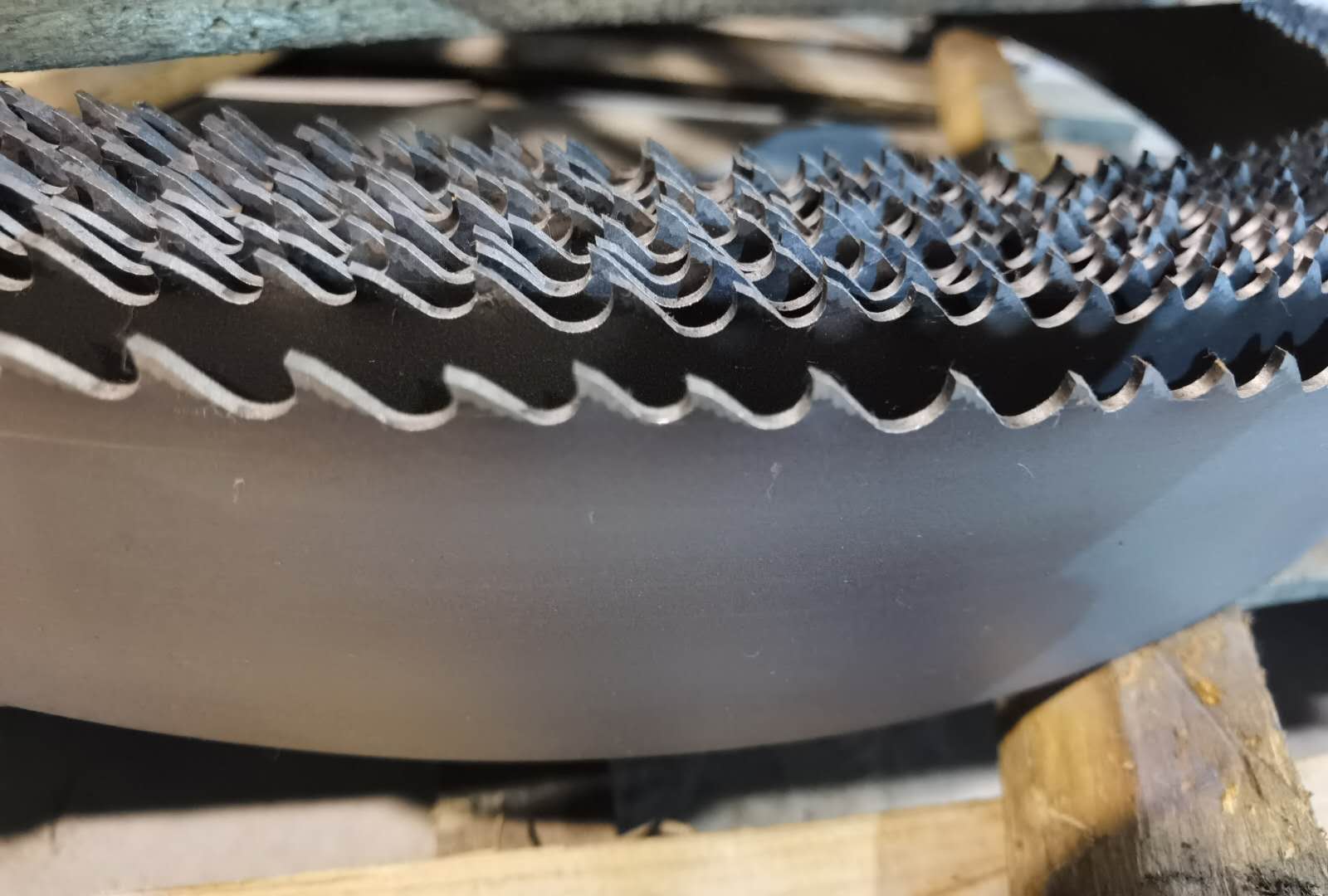
M42 Bimetal Band Saw Blade
Lorem ipsum dolor sit amet, consectetur adipiscing elit. Ut elit tellus, luctus nec ullamcorper mattis, pulvinar dapibus leo.
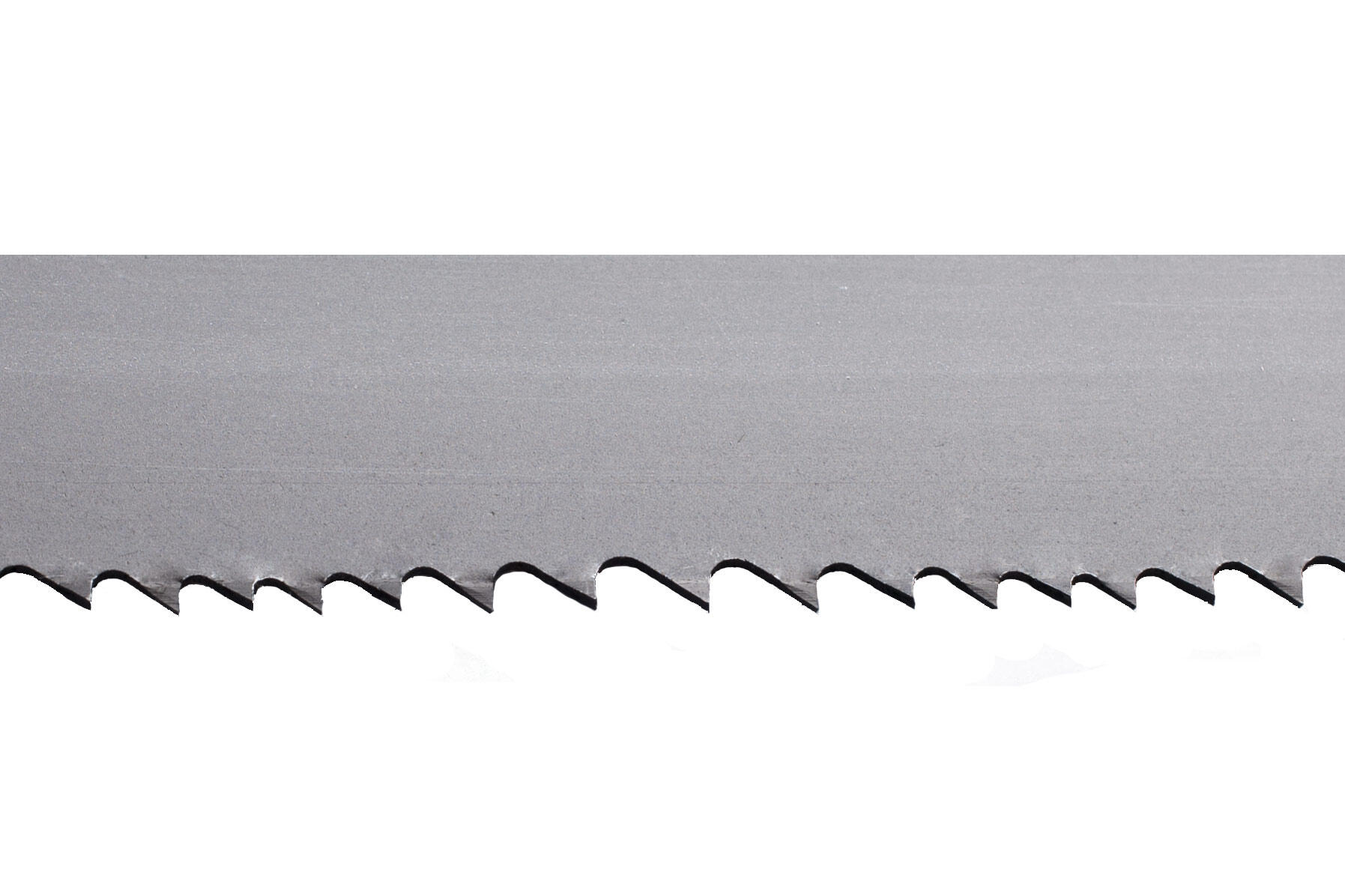
M51 Band Saw Blade
Lorem ipsum dolor sit amet, consectetur adipiscing elit. Ut elit tellus, luctus nec ullamcorper mattis, pulvinar dapibus leo.
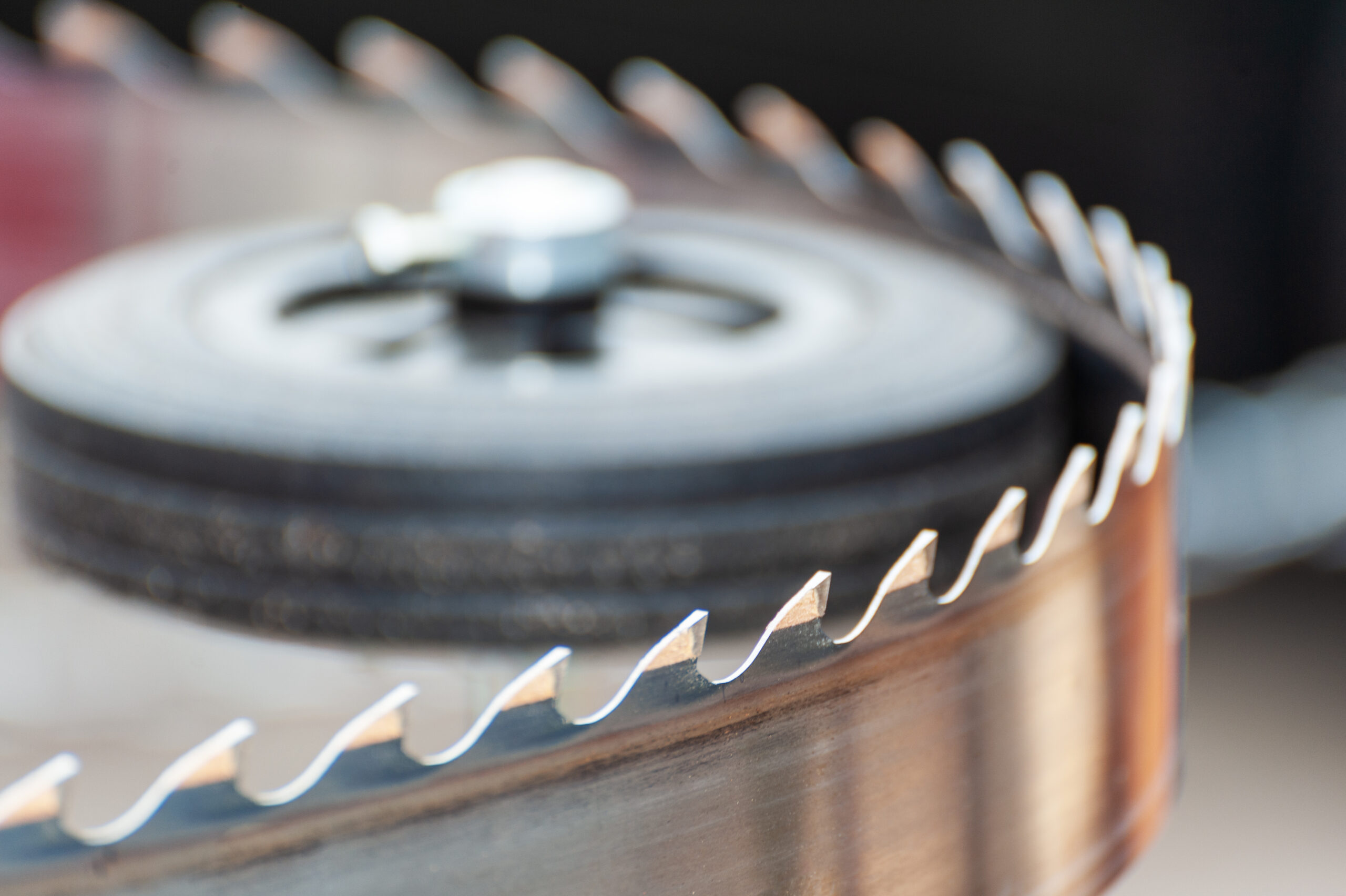
Carbide Tip Band Saw Blade
Carbide tipped band saw blades are made to put up with the intense heat that is generated when cut high-temperature alloys and exotic metals. Each tooth has a multi-chip grind on it, so you get a nice, smooth, clean finish as the blade cuts through the material.
Customize Band Saw Blade for Your Cutting!
At YISHAN, we understand the importance of reliable, high-performance bi-metal bandsaw blades tailored to your market needs. As a trusted leader in bandsaw blade manufacturing, we offer precise customization and fast delivery to meet your specific requirements. Our commitment to quality ensures that you receive top-tier products, backed by expert technical support to help you succeed with every cut.
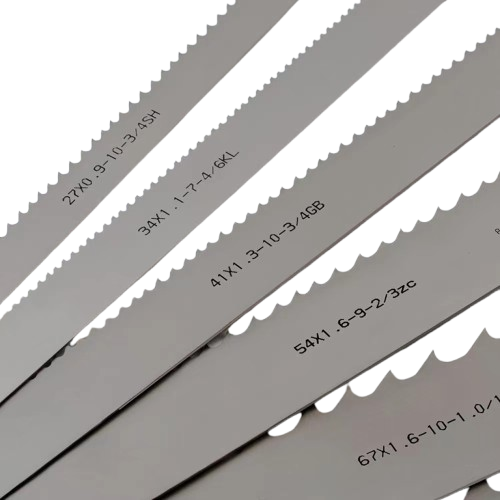
Our metal bandsaw blades are available in durable M42, M51 and Carbide options, customized to fit your specific applications and maximize blade lifespan.
13 x 0.65mm
19 x 0.9mm
27 x 0.9mm
34 x 1.1mm
41 x 1.3mm
54 x 1.6mm
67 x 1.6mm
80 x 1.6mm
0.75/1.25 1/1.5 1.4/2. 1.7/2.5. 2/3
3/4 4/6 5/8 6/10 8/12 10/14 14/18
- Uncoated: Standard option for general-purpose cutting.
- TiN Coating: Increases surface hardness and wear resistance, good for cutting abrasive materials.
- TiCN Coating: Enhanced wear resistance, suitable for cutting hard and abrasive metals.
- Customized to fit specific band saw machines.
- Available in pre-cut lengths or in bulk coil form (e.g.,50meters,100 meters coils) for on-site cutting.
More Than Your Typical Band Saw Blade Manufacturer
At YISHAN, we do more than supply high-quality bi-metal bandsaw blades. We deliver cutting solutions crafted to meet the specific needs of your business. With a focus on precision engineering, durability, and efficient cutting performance, our commitment to quality has made us a trusted partner in the bandsaw blade industry.
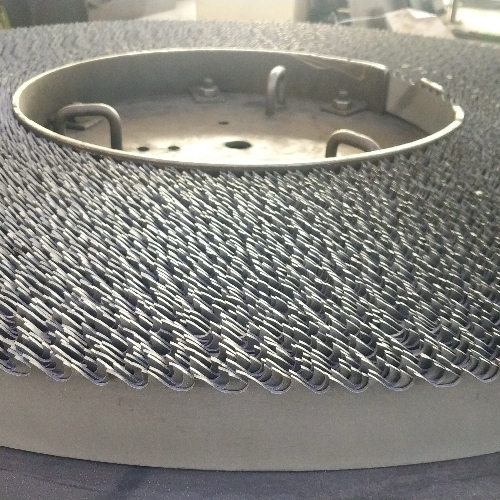
Expert Guidance on Material Selection
Not sure which bi-metal bandsaw blade – be it M42, M51, or carbide blade – is right for your needs? Let our experts guide you to the ideal blade, ensuring your cutting operations run smoothly and efficiently across any material or application.
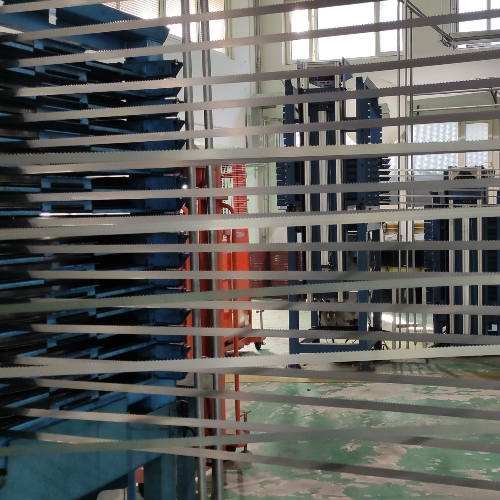
Advanced Manufacturing Expertise
With over a decade of experience in manufacturing band saw blades, we bring precision and expertise to every blade we produce. Whether you're looking for specific tooth configurations, lengths, or custom coatings, we take pride in crafting blades to the highest standards, ensuring durability and performance for every cutting.
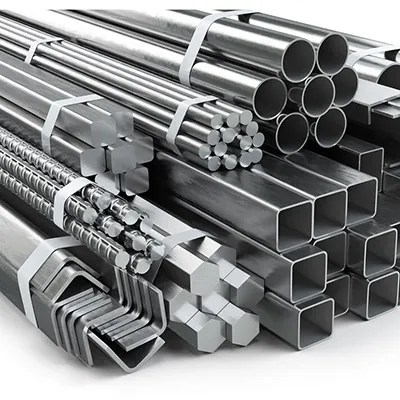
Suitable for all kinds of metal processing
No matter ferrous metal such as ,cast iron, carbon steel, hardened tool steel, stainless steel, pipes & tubes; or non-ferrous metal like aluminum, brass, or other mild steels, we have the right bimetal band saw blade for you.
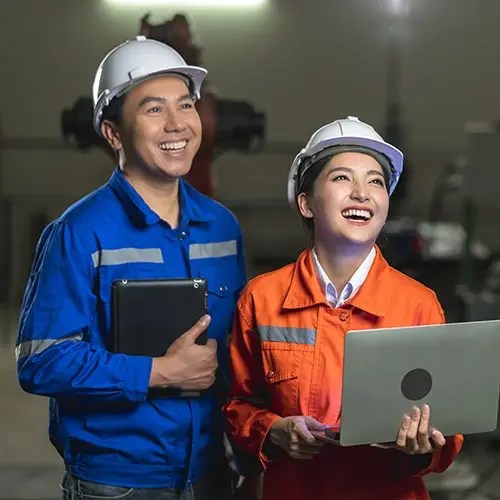
Unmatched Technical Support
Whether you need guidance on blade selection, technical specifications, or performance optimization, we’re here to offer full technical support. From initial consultation to on-site assistance, our team is dedicated to making sure your bi-metal bandsaw blades deliver the reliability and precision you expect—every time.
Why choose YISHAN band saw blade
At YISHAN, we combine over a decade of expertise with a commitment to delivering top-tier bi-metal band saw blades for a wide range of cutting applications. Our focus on custom solutions ensures that each blade is tailored to your exact requirements, making us the trusted partner for your distribution needs. When you partner with us, you’re choosing industry-leading quality, fast delivery, and exceptional customer service, every time.
Adaptable Order Sizes
Whether you need a single bi-metal bandsaw blade or a bulk order, our flexible production capabilities allow us to handle projects of any size with efficiency and speed, ensuring timely delivery without compromising on quality.
Precision Engineering
Whether you need a single bi-metal bandsaw blade or a bulk order, our flexible production capabilities allow us to handle projects of any size with efficiency and speed, ensuring timely delivery without compromising on quality.
Cost-Effective Solutions
Our strategic approach ensures that you receive high-quality titanium baskets at competitive prices, maximizing value without compromising quality.
Comprehensive Saw Blade Expertise
Equipped with cutting-edge machinery, YISHAN offers a full range of saw blade solutions, making us a one-stop shop for all your saw blade needs, from bimetal to other custom components.
Reliable and On-Time Delivery
With a streamlined production process and constant operational efficiency, we guarantee prompt delivery, keeping your projects on track.
Client-Centered Approach
At YISHAN, your satisfaction is our priority. We simplify the purchasing process, offer clear communication, and ensure every product is made to meet your exact requirements.
Your Definitive Guide to Procuring Bi-Metal Band Saw Blades
Bi-metal band saw blades are a must-have tool for many industries, such as metal fabrication, automotive, aviation woodworking, and construction.
Whether you’re looking to find a source of bi-metal band saw blades for your specific cutting applications or expand your wholesale distribution network, this guide will give you all the crucial details you need to make an informed decision. Material grades, tooth configurations, customization options, and technical specifications are all covered.
Chapter 1
What is a Bi-metal Band Saw Blade
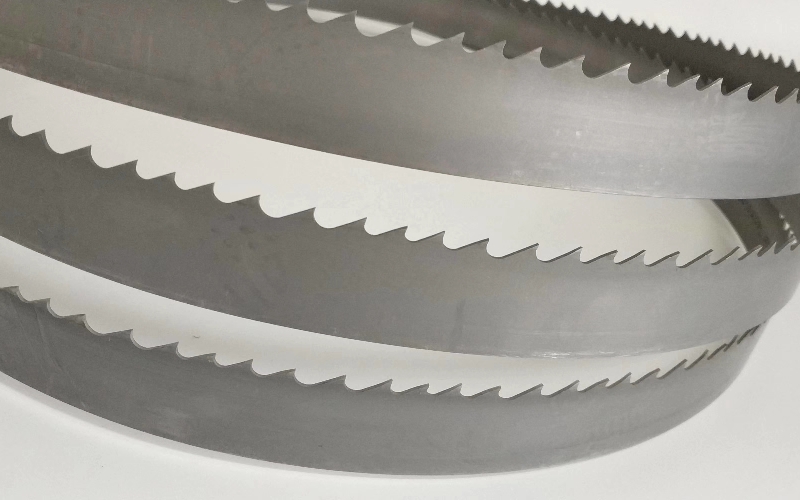
A bi-metal bandsaw blade is a tough, high-performance cutting tool primarily used in the metal fabrication, woodworking, and construction industries.
Made with a high-speed steel tooth edge welded to a flexible alloy steel back, these blades are designed to cut through a wide variety of materials, providing long-lasting durability and superior performance even in the most demanding cutting applications.
Bi-metal bandsaw blades are available in a wide array of options, including different tooth pitches, blade widths, and coatings, to meet the specific needs of multiple industries. They are essential for getting clean, accurate cuts and maximizing your efficiency.
Chapter 2
Key Features of Bi-metal Band Saw Blade
1. High Wear Resistance:The blade has a high-speed steel (HSS) cutting edge,
typically made of M42 or M51 steel, welded onto a flexible spring steel (backing material). This provides excellent resistance to heat and wear.
2. Flexibility & Durability:The backing material (usually high alloy steel) offers good flexibility, reducing the risk of breakage and allowing for a longer lifespan.
3. Versatile Cutting:Suitable for cutting a wide range of materials, from soft metals (like aluminum) to hard alloys (stainless steel, tool steel):Can handle different shapes: bars, tubes, pipes, and structural materials.
4. High Cutting Performance:The HSS cutting edge (e.g., M42 with 8% cobalt) provides high hardness (68-69 HRC), which enables faster cutting speeds and efficiency.
5. Tooth Design Options:Available in a variety of tooth patterns (e.g., variable pitch, hook, or raker teeth) to suit different cutting applications and reduce vibration.
6. Heat Resistance:The HSS edge has excellent heat resistance, allowing for cutting at higher speeds without premature wear.
7. Cost-Effectiveness:Although initially more expensive than carbon steel blades, the longer blade life and higher cutting efficiency make bi-metal blades cost-effective in the long run.
Chapter 3
Bimetal Band Saw Blade Specifications
Specification | Description |
---|---|
Cutting Edge Material | M42 (8% Cobalt), M51 (10% Cobalt), Tungsten Carbide |
Backing Material | High alloy steel (X32,B318) |
Width | 13mm (1/2″),19mm (3/4″), 27mm(1″),34mm(1-1/4″), 41mm(1-1/2″),54mm(2″),67mm(2-5/8″),80mm(3-1/8″) |
Thickness | 0.6 mm, 0.9 mm, 1.1 mm, 1.3 mm, 1.6 mm |
Tooth Pitch (TPI) | 2-3, 3-4, 4-6, 5-8, 6-10 |
Tooth Form | Raker, Hook, Variable |
Edge Hardness | M42: 68-69 HRC M51: 69-70 HRC |
Blade Length | Customizable, Common Coil Lengths: around 100 meters |
Applications | General Metal Cutting, Structural Steel, Stainless Steel, Tool Steel,etc |
Chapter 4
Applications of Bi-metal Band Saw Blade
Bi-metal band saw blades are widely used across various industries due to their durability, versatility, and ability to cut a broad range of materials. Here are some common applications:
1. Metalworking and Fabrication
Cutting Structural Steel: Ideal for cutting beams, channels, and angles used in construction and manufacturing.
Bar Stock Cutting: Efficient for cutting round, square, and rectangular bars made of carbon steel, stainless steel, or alloy steel.
Tube and Pipe Cutting: Suitable for thin-walled and thick-walled tubing, including stainless steel and other difficult-to-cut alloys.
2. Automotive Industry
Used for cutting metal components such as shafts, gears, and engine parts.
Suitable for cutting hardened steels and high-performance alloys used in automotive applications.
3. Aerospace Industry
Ideal for cutting high-strength alloys, including titanium, Inconel, and other aerospace-grade materials.
Provides precision and high surface finish required for aerospace components.
4. Tool and Die Making
Used for cutting tool steels like D2, H13, and other high-hardness materials required in tool manufacturing.
Suitable for cutting blanks, molds, and dies with high precision.
5. Maintenance and Repair (MRO)
Widely used in maintenance workshops for cutting a variety of materials during repairs and fabrication work.
Versatile enough for both solid and hollow sections, making it a reliable choice for general-purpose cutting.
6. Foundry and Forging
Efficient for cutting cast iron, forged parts, and rough surfaces.
Capable of handling high-temperature materials and abrasive surfaces found in foundry applications.
7. Pipe and Tube Mills
Commonly used in production lines for cutting pipes and tubes made of steel, stainless steel, and non-ferrous metals.
Provides high-speed cutting and long blade life, reducing downtime in continuous operations.
8. Metal Recycling
Suitable for cutting scrap metal, including mixed materials and unknown grades of metal.
Handles diverse shapes and sizes, from thin sheet metal to heavy, solid bars.
Chapter 5
Customization Bi-metal Band Saw Blade Options
Customization of bi-metal band saw blades is often needed to optimize performance for specific materials and cutting applications. Here are the typical customization options available:
1. Blade Material Selection
M42 (HSS Edge): Standard choice for most metal cutting, with high cobalt content (8%) for better wear resistance.
M51 (HSS Edge): Enhanced performance with higher cobalt (10%) and tungsten (10%) content, ideal for cutting tough, high-hardness materials like Inconel, titanium, and hardened steel.
2. Width and Thickness
Custom Width: From 13 mm (1/2″) to 80 mm (3-1/8″), depending on the type of cutting machine and workpiece size.
Custom Thickness: Options like 0.6 mm, 0.9 mm, 1.1 mm, 1.3 mm, and 1.6 mm to match the rigidity needed for different material thicknesses and applications.
3. Tooth Pitch (TPI)
Variable TPI: For mixed cutting tasks, reducing vibration and providing smoother cuts (e.g., 4-6 TPI, 5-8 TPI).
Fixed TPI: For consistent cutting of uniform materials (e.g., 2-3 TPI for thick solids, 6-10 TPI for thin-walled tubing).
Ultra-Fine Pitch: For cutting small, delicate parts or thin-walled tubing.
4. Tooth Form
Hook Tooth: Aggressive tooth angle for fast cutting of thick, solid materials.
Raker Tooth: Alternating set teeth, suitable for general-purpose cutting of a wide range of metals.
Variable Tooth: Reduces vibration and noise, enhances surface finish, ideal for mixed materials.
5. Coating Options
TiN (Titanium Nitride) Coating: Increases surface hardness and wear resistance, good for cutting abrasive materials.
TiCN (Titanium Carbonitride) Coating: Enhanced wear resistance, suitable for cutting hard and abrasive metals.
Uncoated: Standard option for general-purpose cutting.
6. Blade Length
Customized to fit specific band saw machines.
Available in pre-cut lengths or in bulk coil form (e.g., 100 meterscoils) for on-site cutting.
7. Special Tooth Geometry
Custom tooth angles and shapes can be designed based on specific applications (e.g., negative rake angle for hard, brittle materials).
8. Weld Quality
Special Weld Joints: Reinforced welds for improved strength and durability, especially in high-tension applications.
9. Edge Hardness
Customized Edge Hardness: Tailored to the material being cut, typically ranging from 68-70 HRC depending on the bi-metal type (e.g., M42 or M51).
10. Packaging and Branding
Custom packaging options for bulk orders.
Branding with the customer’s logo and specifications printed on the blade.
These customization options allow bi-metal band saw blades to be tailored to specific industrial requirements, ensuring optimal cutting performance, blade life, and cost-efficiency.
Chapter 6
Maintenance and Care of Bi-metal Band Saw Blade
Proper maintenance and care of bi-metal band saw blades can significantly extend their life, improve cutting performance, and reduce costs. Here are key tips for ensuring optimal blade performance:
1. Break-In Procedure
For a new blade, use a break-in procedure to gradually wear the teeth. Start with reduced cutting speed and feed rate (about 50% of normal feed rate) for the first 15-30 minutes.
This helps avoid chipping of the new teeth and extends the blade life.
2. Proper Blade Tension
Ensure the blade is properly tensioned according to the manufacturer’s specifications (typically 25,000 to 30,000 psi).
Under-tensioning can cause the blade to slip, while over-tensioning can lead to blade breakage.
3. Blade Tracking and Alignment
Check the alignment and tracking of the blade on the band saw machine. The blade should run straight and not drift off-center.
Misalignment can cause uneven wear and premature tooth damage.
4. Use the Right Cutting Speed and Feed Rate
Select the correct cutting speed and feed rate based on the material being cut:
Hard materials (e.g., stainless steel, tool steel): Lower speed, higher feed rate.
Soft materials (e.g., aluminum, mild steel): Higher speed, lower feed rate.
Refer to the manufacturer’s guidelines for speed and feed recommendations.
5. Lubrication and Coolant
Use appropriate cutting fluids or coolants to reduce heat buildup and friction.
Proper lubrication minimizes blade wear, improves surface finish, and prevents tooth chipping, especially when cutting hard or abrasive materials.
6. Clean the Blade Regularly
Remove chips and debris from the blade and saw guides frequently. Accumulated chips can cause tooth damage and affect cutting performance.
Use a chip brush or air blower to clear chips during operation.
7. Inspect the Blade Regularly
Check the blade for signs of wear, such as:
Tooth dulling or rounding.
Cracks on the back edge of the blade.
Chipped or broken teeth.
Replace the blade if any of these issues are detected to prevent further damage and poor cuts.
8. Proper Storage
Store blades in a dry and clean environment to prevent rust.
Hang coils on a peg or store them in a flat position to avoid bending or kinking.
9. Avoid Excessive Blade Vibration
Excessive vibration can cause uneven wear and reduce blade life.
Use a variable pitch tooth design or adjust the feed rate to minimize vibration.
10. Use Appropriate Blade for the Material
Choose the right blade material (e.g., M42 or M51) and tooth configuration based on the material being cut.
Using an inappropriate blade type can lead to rapid wear and damage.
By following these maintenance tips, you can ensure consistent performance, longer blade life, and improved cutting quality for your bi-metal band saw blades.
Chapter 7
How to Find a Reliable Bi-metal Band Saw Blade Manufacturer?
Finding a reliable bi-metal band saw blade manufacturer is crucial for ensuring consistent quality, reliable supply, and excellent customer support. Here’s a guide on how to identify the right supplier for your needs:
1. Check Product Quality and Certifications
-
Look for manufacturers with ISO 9001 or other quality certifications. This indicates adherence to international standards.
-
Inquire about the materials used and whether they source from reputable suppliers.
-
Request sample blades and conduct tests to evaluate cutting performance, durability, and surface finish.
2. Evaluate Technical Expertise
-
Choose a manufacturer with strong R&D capabilities and a good track record in product innovation.
-
They should offer a range of customization options (e.g., special coatings, tooth geometry) and be able to provide expert recommendations based on your application needs.
3. Assess Manufacturing Capacity and Lead Times
-
Confirm the production capacity to ensure they can handle your order volume, whether it’s small batch orders or large bulk orders.
-
Check lead times, especially if you require frequent or large orders. Reliable manufacturers should have efficient production processes and reasonable delivery times.
4. Look for Comprehensive Product Range
-
A good manufacturer should offer a wide selection of blade types, including:
-
Standard M42 and M51 bi-metal blades.
-
Specialty blades for specific applications (e.g., pipe cutting, hardened steel).
-
Customizable options in terms of width, thickness, TPI, and tooth forms.
-
5. Check Customer Reviews and References
-
Look for customer testimonials and case studies. Positive feedback from other users in similar industries can be a good indicator of quality and reliability.
-
Ask for references and contact existing clients to get direct feedback about their experience with the manufacturer.
6. Inspect Customer Support and After-Sales Service
-
Reliable manufacturers provide strong technical support, including assistance with product selection, troubleshooting, and blade maintenance advice.
-
Ensure they offer after-sales service, such as handling claims, replacements for defective blades, and technical consultations.
7. Consider Price vs. Value
-
While pricing is important, don’t compromise on quality. Cheaper blades might have a shorter lifespan, leading to more frequent replacements and higher long-term costs.
-
A reliable manufacturer offers a good balance of competitive pricing and consistent quality.
8. Verify Global Presence and Distribution Network
-
If you have operations in multiple regions, consider a manufacturer with a global presence or a strong distribution network. This ensures easier access and faster delivery.
-
Local distributors and partners can also provide quicker support and service.
9. Check for Industry Experience
-
Look for a manufacturer with extensive experience in producing bi-metal band saw blades, preferably over a decade. Experienced companies are more likely to have refined their production processes and quality control.
10. Visit the Manufacturer (If Possible)
-
If feasible, arrange a visit to the production facility to inspect the manufacturing process, quality control measures, and overall operations.
-
A factory visit can give you insights into their production capabilities, technology, and commitment to quality.
Red Flags to Watch Out For:
-
Inconsistent product quality.
-
Lack of transparency in pricing and material sourcing.
-
Poor communication or delayed responses from the sales team.
-
Limited or no after-sales support.
By considering these factors, you can find a reliable bi-metal band saw blade manufacturer that meets your quality standards and supports your business needs.
Chapter 8
Precautions for Using Bi-metal Band Saw Blade
Using a bi-metal band saw blade requires specific precautions to ensure safe operation, optimal performance, and longer blade life. Here are some key precautions to take:
1. Follow the Break-In Process
Always follow the break-in procedure for new blades. Start with a reduced feed rate and speed for the first 15-30 minutes.
Gradually increase to normal cutting parameters after the teeth have been properly worn in. This helps prevent premature tooth damage.
2. Select the Right Blade for the Material
Use a blade with the appropriate tooth pitch, material (e.g., M42 or M51), and tooth form for the specific application.
Incorrect blade selection can lead to poor performance, excessive wear, and potential blade breakage.
3. Check Blade Tension Regularly
Ensure the blade tension is set according to the manufacturer’s specifications (typically 25,000 to 30,000 psi).
Under-tensioned blades can slip or produce inaccurate cuts, while over-tensioned blades may break.
4. Ensure Proper Machine Setup
Verify that the band saw machine is properly set up, including blade guides, bearings, and tracking alignment.
Misalignment can cause the blade to twist or bend, leading to uneven wear or breakage.
5. Use Correct Cutting Speed and Feed Rate
Adjust the cutting speed and feed rate based on the material’s hardness and thickness:
High speed, low feed for soft metals (e.g., aluminum).
Low speed, high feed for hard metals (e.g., stainless steel, tool steel).
Incorrect settings can lead to blade overheating, tooth damage, and poor cut quality.
6. Apply Proper Lubrication and Coolant
Always use an appropriate cutting fluid or coolant to reduce heat and friction.
Insufficient lubrication can lead to excessive wear, blade overheating, and tooth chipping, especially with hard-to-cut materials.
7. Avoid Excessive Force
Do not apply excessive force when feeding the material into the blade. Let the blade do the cutting.
Excessive force can cause the blade to deflect, resulting in inaccurate cuts and potential breakage.
8. Monitor for Signs of Wear and Damage
Regularly inspect the blade for signs of wear, such as dull teeth, cracks, or chipped teeth.
Replace the blade immediately if you notice significant wear or damage to avoid damaging the workpiece or machine.
9. Remove Chips and Debris Frequently
Use a chip brush or air blower to keep the blade and work area free of chips and debris.
Accumulated chips can cause tooth breakage and affect the quality of the cut.
10. Store Blades Properly
Store unused blades in a dry, clean area. Hang coils vertically or lay them flat to prevent bending or kinking.
Rust or deformation from improper storage can compromise blade performance.
11. Wear Appropriate Personal Protective Equipment (PPE)
Always wear safety goggles, gloves, and hearing protection when operating a band saw machine.
Protect yourself from sharp blade edges, flying debris, and noise.
12. Never Operate with a Damaged Blade
If the blade shows any sign of cracks, missing teeth, or warping, stop the machine immediately and replace the blade.
Using a damaged blade can lead to accidents and further machine damage.
13. Follow Manufacturer’s Guidelines
Always refer to the manufacturer’s manual for specific recommendations on blade use, machine setup, and maintenance procedures.
Each blade and machine may have unique requirements that need to be followed.
By following these precautions, you can ensure safer operation, better cutting performance, and extend the lifespan of your bi-metal band saw blade.
Chapter 9
In summary
With over a decade of expertise, YISHANHN delivers top-quality bi-metal bandsaw blades tailored to meet the specific needs of various industries. Our custom solutions guarantee optimal cutting performance and extended blade life, whether for standard or specialized applications. Trust YISHANHN as your reliable partner for premium, customizable bi-metal bandsaw blades.
Custom Your Bi-metal Band Saw Blade Today with Ease!
Whatever your bi-metal bandsaw blade needs, our expertise guarantees precision-engineered solutions tailored to your specifications. By sourcing high-quality raw materials and maintaining rigorous quality control, we deliver exceptional blade performance and longevity. Plus, our streamlined production process allows us to offer competitive pricing, giving you unbeatable value and reliability.
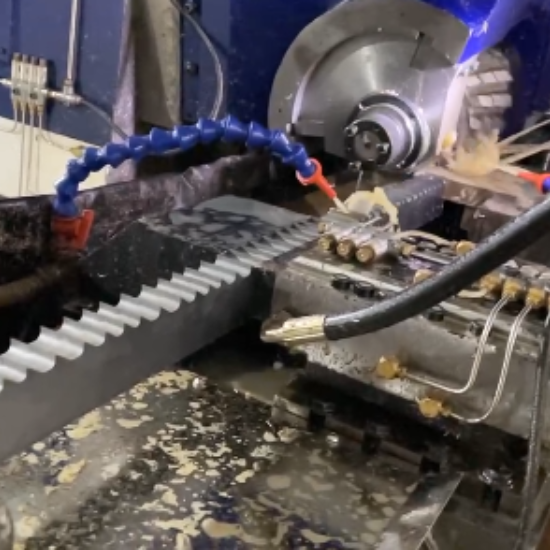
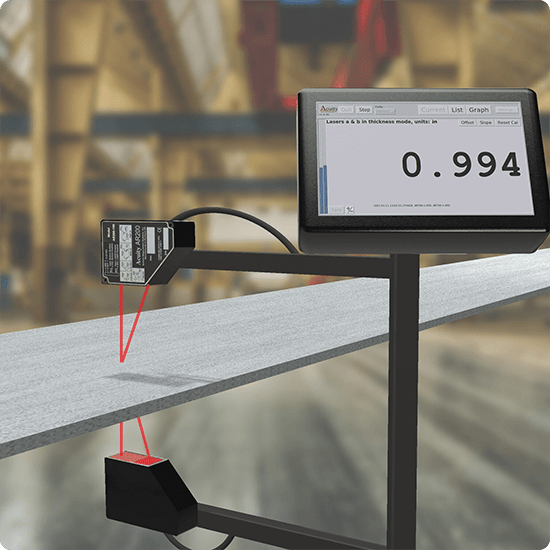