Carbide Band Saw Blade
Searching for premium-quality carbide band saw blades to elevate your cutting performance? Look no further than YISHAN. As experts in the field, we take pride in manufacturing a wide range of top-grade carbide band saw blades, designed in various sizes and specifications to perfectly align with your needs.
Your Reliable Carbide Band Saw Blade Manufacturer
YISHAN is a leading manufacturer of carbide band saw blades in China, specializing in both standard and custom solutions for a variety of cutting applications. We cater to wholesalers, agents, and industrial clients seeking a competitive edge in the marketplace.
We offer a comprehensive range of meat band saw blades in different sizes and specifications to fit your exact needs. With our ISO 9001-certified production process, cutting-edge equipment, and expert craftsmanship, we guarantee precision and quality in every blade we deliver. Trust us to get it right, every time.

Carbide Band Saw Blade
The carbide band saw blade is a high-performance cutting tool with tungsten carbide-tipped teeth, offering exceptional hardness and heat resistance. Ideal for cutting tough materials like hard wood ,hardened steels, titanium, high-temperature alloys, and composites with precision and durability.
Custom Carbide Band saw Blades
Carbide band saw blades, renowned for their durability and precision, are essential for cutting tough materials like hardened steel and composites. As a leading carbide blade manufacturer in China, YISHAN provides customized solutions, from general-purpose to specialized blades. Explore our offerings and contact us today for tailored cutting solutions!
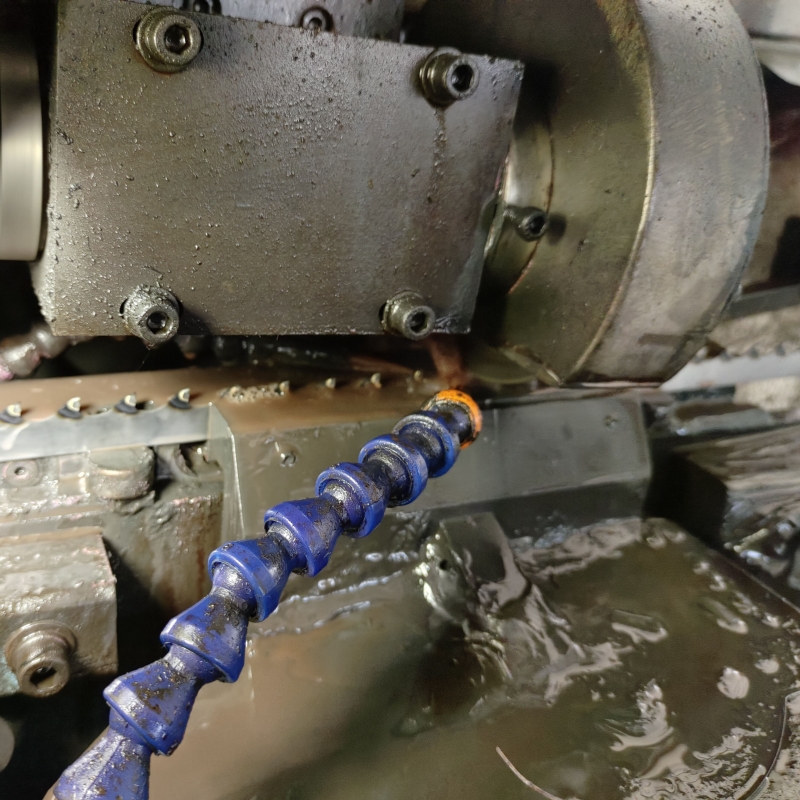
Our metal bandsaw blades are available in durable M42, M51 and Carbide options, customized to fit your specific applications and maximize blade lifespan.
13 x 0.5mm
16×0.46mm
16×0.5mm
16×0.56mm
19×0.56mm
19×0.6mm
Variable teeth or Standard teeth
Teeth distance: from 12mm to 35mm
- Customized to fit specific band saw machines.
- Available in pre-cut lengths or in bulk coil form (e.g.,50meters,100 meters coils) for on-site cutting.
Why choose YISHAN band saw blade
Since 2012, YISHAN has been a trusted name in carbide band saw blade manufacturing, known for precision, quality, and reliability. Our advanced in-house facilities and skilled engineers enable us to supply cutting solutions for industries like metalworking, engineering, and manufacturing.
Adaptable Order Sizes
Whether you need a single carbide band saw blade or a bulk order, our flexible production capabilities allow us to handle projects of any size with efficiency and speed, ensuring timely delivery without compromising on quality.
Precision Engineering
With over 18 years of experience, our skilled engineers excel at manufacturing carbide band saw blades that meet the highest industry standards, ensuring maximum performance and long-lasting durability.
Cost-Effective Solutions
Our strategic approach ensures that you receive high-quality titanium baskets at competitive prices, maximizing value without compromising quality.
Comprehensive Saw Blade Expertise
Equipped with cutting-edge machinery, YISHAN offers a full range of saw blade solutions, making us a one-stop shop for all your saw blade needs, from bimetal to other custom components.
Reliable and On-Time Delivery
With a streamlined production process and constant operational efficiency, we guarantee prompt delivery, keeping your projects on track.
Client-Centered Approach
At YISHAN, your satisfaction is our priority. We simplify the purchasing process, offer clear communication, and ensure every product is made to meet your exact requirements.
Your Comprehensive Guide to Carbide Band Saw Blade
Carbide band saw blades are used in all sorts of industries: metalworking, construction, manufacturing, etc. If you want to import high-quality carbide blades to sell in your market, you’re in the right place. This guide will give you all the information you need to make good decisions about where to get carbide band saw blades.
Chapter 1
What is a Carbide Band Saw Blade
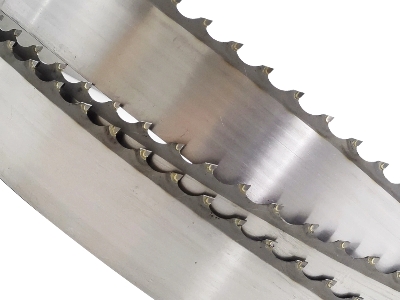
Carbide band saw blade is a special type of saw blade that has carbide teeth or a carbide edge on it for cutting tough, abrasive materials. Carbide is a compound of tungsten and carbon. It’s extremely hard and has a great wear resistance. That’s why these blades are perfect for applications where regular steel blades won’t work.
Chapter 2
Key Features of Carbide Band Saw Blade
Exceptional Hardness
- Tungsten carbide-tipped teeth maintain sharpness longer than other blade materials.
Heat Resistance
- Handles high cutting speeds and elevated temperatures without losing performance.
Wear Resistance
- Designed to cut abrasive and tough materials with minimal tooth wear.
Precision Cutting
- Delivers accurate and clean cuts, reducing material waste.
Durability
- Longer blade life compared to bimetal or carbon steel blades, even in demanding applications.
Versatility
- Suitable for cutting hard metals (hardened steel, alloys), non-ferrous materials (aluminum, brass), and composites.
Low Vibration
- Enhanced stability minimizes blade deflection, ensuring smoother cuts.
These features make carbide band saw blades ideal for industries requiring efficient, high-precision cutting in challenging environments.
Chapter 3
Carbide Band Saw Blade Specifications
Specification | Description |
---|---|
Material | High-alloy steel body with tungsten carbide-tipped or carbide-coated teeth. |
Length | Customizable, Common Coil Lengths: around 100 meters |
Width | 15 mm to 125 mm , depending on machine and cutting application. |
Thickness | 0.5 mm to 1.6 mm (0.02″ to 0.063″) |
Tooth | Variable, standard, or custom for optimized cutting performance. |
Packing | 10 blades per box |
Hardness | 70-91HRC |
Meat Band Saws / Bone Saw Machines | Universal any brands such as: Biro ,Thompson,Kolbe,Torrey,Butcher Boy,Hobart,Skyfood Equipment etc |
Applications | Metals, composites, hard woods, alloys, and other tough materials. |
Chapter 4
Applications of Carbide Band Saw Blade
Carbide band saw blades are designed for demanding cutting applications where precision, durability, and high performance are essential. Their applications include:
1. Metal Cutting
Exotic Alloys: Titanium, Inconel, Hastelloy, and other heat-resistant alloys.
Hardened Materials: High-speed steel (HSS), case-hardened steels, and tool steels.
Non-ferrous Metals: Aluminum, copper, and brass in bulk cutting.
2. Woodworking
Hardwoods and Abrasive Woods: Dense species like teak, maple, and tropical hardwoods.
Composite Materials: MDF, plywood, and laminated panels.
3. Plastics and Composites
Reinforced Plastics: Fiberglass and carbon-fiber composites.
Abrasive Plastics: Acrylics, PVC, and other engineered plastics.
4. Abrasive Materials
Ceramics: Cutting porous ceramics or similar materials.
Graphite: For high-temperature industrial components.
5. Production and Manufacturing
Automotive: Cutting high-performance components.
Aerospace: Shaping critical components from exotic materials.
The carbide teeth maintain sharpness longer and withstand extreme heat and wear, making them ideal for precision and industrial-grade operations.
Chapter 5
Customization Carbide Band Saw Blade Options
Customizing carbide band saw blades allows tailoring their performance for specific applications. Here are the main customization options:
1. Tooth Geometry
Pitch (TPI): Adjusted for material thickness and type (e.g., coarse pitch for thick materials, fine pitch for thin materials).
Tooth Shape: Alternate or standard
2. Blade Width and Thickness
Wider blades for straight cuts; narrower blades for contour cutting.
Adjust thickness to balance strength and flexibility for specific applications.
3. Carbide Grade
General Purpose: For diverse materials.
Special Grades: Enhanced wear resistance for abrasive materials or improved toughness for impact-prone operations.
4. Coatings
TiN (Titanium Nitride): Reduces friction and increases wear resistance.
TiAlN (Titanium Aluminum Nitride): For high-temperature cutting.
Diamond Coating: For cutting highly abrasive materials like composites or ceramics.
5. Blade Length
Tailored to specific band saw machines or cutting setups.
6. Kerf Width
Optimized for material conservation or cutting speed.
7. Application-Specific Adjustments
Noise Reduction: Special tooth profiles or backer treatments.
Vibration Resistance: Advanced tensioning for stable cuts.
By selecting the right combination of features, customized carbide band saw blades ensure efficiency, longevity, and precision for unique operational requirements.
Chapter 6
Maintenance and Care of Carbide Band Saw Blade
Proper maintenance and care of carbide band saw blades are essential for maximizing their lifespan and maintaining cutting performance. Here are key practices:
1. Regular Cleaning
Remove Debris: After each use, clean the blade to remove chips, dust, and resin buildup.
Use Non-Abrasive Cleaners: Avoid harsh chemicals that can damage the carbide teeth or coating. A simple brush or compressed air can often suffice.
2. Blade Tensioning
Correct Tension: Ensure the blade is properly tensioned to prevent warping or uneven wear. Check the manufacturer’s specifications.
Avoid Over-Tensioning: Too much tension can cause premature tooth wear or breakage.
3. Lubrication and Cooling
Proper Lubricant: Use a recommended cutting fluid or coolant to reduce friction, cool the blade, and flush away debris.
Temperature Control: Carbide blades are highly sensitive to heat. Keep the cutting temperature within recommended limits to prevent tooth damage.
4. Tooth Inspection
Inspect Regularly: Check the carbide teeth for signs of wear, chipping, or breakage. Look for any signs of dullness or damage, especially if cutting hard or abrasive materials.
Sharpening: If necessary, have the blade professionally sharpened. Carbide blades cannot be resharpened by conventional methods but may be reground or retipped by specialized services.
5. Proper Storage
Avoid Rust: Store blades in a dry, cool environment to avoid corrosion, especially if the blade is unused for extended periods.
Keep Blades Straight: Ensure the blades are stored in a manner that prevents bending or warping. Hanging them or storing in a rigid, protective case is ideal.
6. Correct Cutting Parameters
Feed Rate: Use the appropriate feed rate for the material and blade type. Too fast a feed rate can cause excessive wear or damage to the carbide teeth.
Cutting Speed: Ensure you’re operating within the recommended speed for the material being cut. Slower speeds may cause overheating, while too fast can result in wear.
7. Avoiding Material Build-up
Check for Material Buildup: In some cutting operations, materials can accumulate on the teeth (like resin, pitch, or metal filings). Use a blade cleaner or brush to clear buildup and maintain cutting efficiency.
By following these practices, carbide band saw blades can achieve optimal performance, extend their lifespan, and minimize costly downtime or premature wear.
Chapter 7
How to Find a Reliable Carbide Band Saw Blade Manufacturer?
Finding a reliable carbide band saw blade manufacturer requires careful evaluation based on several key factors. Here’s how to approach the process:
1. Evaluate Industry Reputation
Experience: Look for manufacturers with a proven track record in producing carbide band saw blades. Established companies are more likely to have refined processes and quality control.
Customer Reviews and References: Check reviews, testimonials, and case studies from existing customers. Ask for references and examples of past work, especially for similar applications.
2. Quality Certifications
ISO 9001: Certification for quality management systems ensures the manufacturer adheres to high production standards.
3. Product Range and Customization
Customization Options: A reliable manufacturer should offer a range of customizable options (e.g., tooth geometry, coating, carbide grades) tailored to your specific needs.
Product Variety: Ensure they offer carbide blades for the materials and industries you work with, such as metals, wood, plastics, or composites.
4. Manufacturing Capabilities
Advanced Technology: Look for manufacturers who use state-of-the-art technology, such as CNC machines, precision grinding, and coating techniques. This ensures consistency and accuracy in blade production.
In-House R&D: Manufacturers with a research and development team can offer innovative solutions and continuous improvement to their products.
5. Lead Time and Availability
Delivery Time: Choose a manufacturer with reliable lead times, especially if you have urgent or high-volume orders.
Stock Availability: Check if they keep a sufficient stock of standard blades and offer quick turnaround times for custom orders.
6. After-Sales Support
Warranty and Maintenance Services: Ensure the manufacturer offers warranties on their products and has a reliable system in place for repairs, sharpening, and blade maintenance.
Technical Support: A good manufacturer will provide technical guidance for selecting the right blade, optimizing cutting conditions, and troubleshooting issues.
7. Cost vs. Quality
Competitive Pricing: While price is important, avoid manufacturers who only focus on low cost at the expense of quality. Higher quality carbide blades will reduce overall operational costs by offering better durability and fewer replacements.
Transparent Pricing: Make sure all costs, including shipping and potential customization fees, are clear upfront.
8. Production Location and Communication
Location: Consider proximity if you need faster shipping or wish to visit the manufacturing site. Domestic manufacturers may offer faster lead times, but reliable overseas suppliers can often provide competitive pricing.
Clear Communication: Choose a manufacturer who is responsive and communicates well. The ability to discuss specifications, adjustments, and delivery schedules clearly can save time and prevent mistakes.
9. Trial Orders
Request Samples or Trial Orders: Before making a large investment, request a sample or smaller trial order to evaluate the quality, performance, and durability of the carbide band saw blades.
Test in Real Conditions: Ensure the blades meet your operational needs and perform well with the materials you intend to cut.
10. Sustainability and Ethics
Environmental Practices: Consider manufacturers with sustainable practices, including waste reduction and eco-friendly materials.
Ethical Standards: Look into labor practices and ensure the company follows ethical guidelines in production.
By focusing on these factors, you can identify a reliable and reputable carbide band saw blade manufacturer who meets your quality standards, production requirements, and customer service expectations.
Chapter 8
Precautions for Using Carbide Band Saw Blade
Using carbide band saw blades requires adherence to specific precautions to ensure safety, maximize blade performance, and prevent damage. Here are the key precautions:
1. Proper Installation
Correct Blade Tension: Follow the manufacturer’s recommendations for tensioning to avoid over-tightening or under-tightening. Improper tension can lead to blade breakage or uneven cuts.
Alignment: Ensure the blade is properly aligned with the guide rollers and wheels to prevent uneven wear or blade twisting.
Machine Settings: Adjust feed rate, speed, and blade tracking settings according to the blade type and material being cut.
2. Material Preparation
Secure Material: Clamp or hold the material firmly to prevent movement during cutting.
Clean Workpiece: Remove dirt, oil, or foreign objects from the material to avoid blade contamination or damage.
3. Cutting Conditions
Avoid Excessive Force: Use steady and even pressure during cutting. Forcing the blade can cause tooth chipping or overheating.
Use Coolant or Lubricant: Apply cutting fluid to reduce heat, friction, and wear, especially when cutting metals or abrasive materials.
4. Blade Selection
Material-Specific Blades: Use the correct blade for the material and application to prevent rapid wear or breakage.
Tooth Pitch (TPI): Match the tooth pitch to the material thickness (e.g., fine teeth for thin materials, coarse teeth for thicker materials).
5. Monitor Blade Condition
Check for Damage: Inspect the blade for signs of wear, chipping, or cracks before and after use. Replace damaged blades immediately.
Dull Blades: Do not use a dull blade as it increases cutting resistance, heat, and the risk of accidents.
6. Operational Safety
Wear Protective Gear: Use safety goggles, gloves, and ear protection when operating the machine. Avoid loose clothing that could get caught.
Avoid Blade Contact: Keep hands and tools clear of the blade path during operation. Use push sticks or clamps when necessary.
Power Off During Adjustments: Turn off the machine and disconnect power when changing blades or performing maintenance.
7. Avoid Heat Damage
Prevent Overheating: Avoid prolonged continuous use without breaks, as excessive heat can weaken the carbide teeth and blade material.
Allow Blade to Cool: Let the blade cool naturally after use; rapid cooling (e.g., with water) may cause stress cracks.
8. Storage and Handling
Proper Storage: Store blades in a dry, secure area to prevent corrosion or accidental damage. Hang or lay flat in protective sleeves.
Handle with Care: Avoid dropping or bending the blade during installation or removal to protect the carbide teeth and the blade body.
9. Cutting Parameters
Follow Recommended Speeds: Operate within the specified cutting speed and feed rate for the material. Excessive speed can reduce blade life and cause overheating.
Avoid Sudden Stops: Maintain a steady cutting motion to prevent vibrations or blade stress.
10. Machine Maintenance
Regular Inspection: Check the band saw machine’s guides, bearings, and wheels for wear or misalignment.
Clean Blade Path: Keep the sawdust, chips, and debris out of the machine to prevent clogging or blade interference.
By adhering to these precautions, you can enhance the safety, efficiency, and lifespan of carbide band saw blades while achieving optimal cutting performance.
Chapter 9
In summary
Carbide band saw blades are a high-performance solution for cutting a wide range of materials – including hard metals, exotic alloys, and abrasive composites – with unbeatable durability, precision, and efficiency. Advanced tooth geometries, customizable options, and specially engineered coatings for your specific application mean better cutting performance, less downtime and lower costs.
Custom Your Carbide Band Saw Blade Today with Ease!
Whatever your carbide band saw blade needs, our expertise guarantees precision-engineered solutions tailored to your specifications. By sourcing high-quality raw materials and maintaining rigorous quality control, we deliver exceptional blade performance and longevity. Plus, our streamlined production process allows us to offer competitive pricing, giving you unbeatable value and reliability.
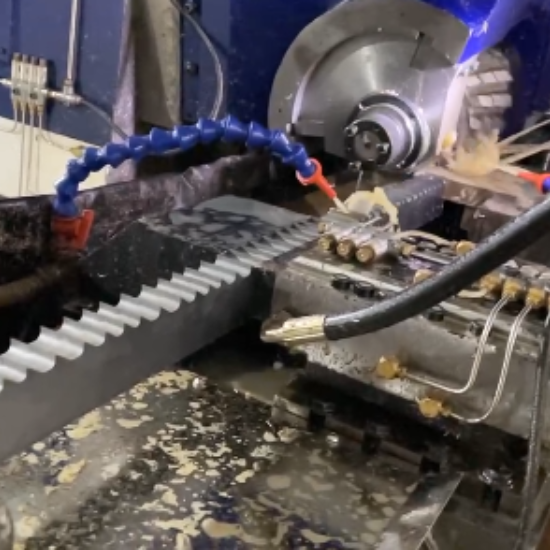
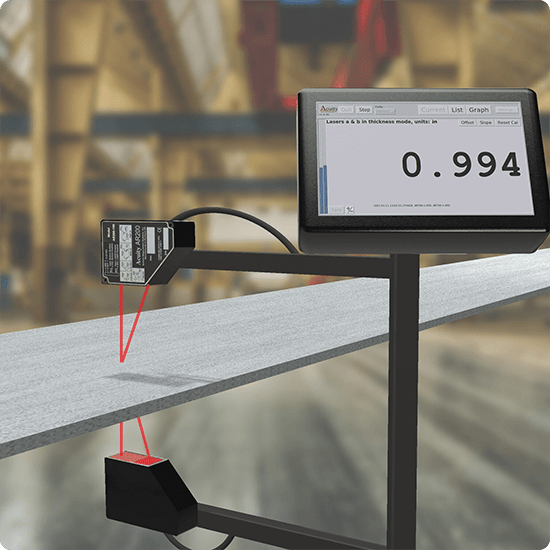